5 Key Steps To An Effective Risk Management Program For Parking Operations
August 19, 2022
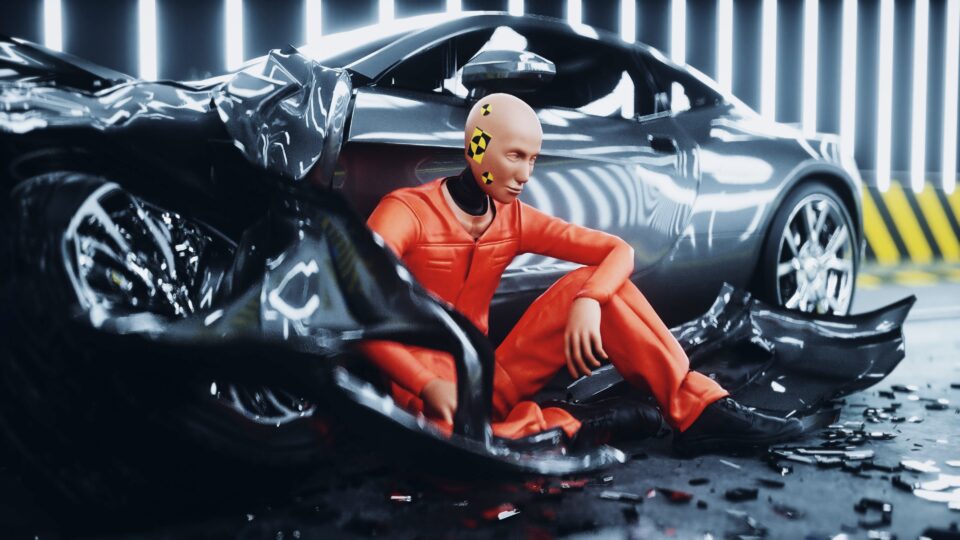
An occupational health and safety plan that is integrated with business operations can reduce the risks of on-premises injuries and worker illnesses.
Many parking industry companies treat the costs of injuries and illnesses as part of doing business, even as these costs have grown significantly in recent years. An employee health and safety plan that is fully integrated into business operations can reduce these risks and associated costs. In 2017, Parking Concepts, Inc. (PCI) implemented such a plan, which led to a more than 80% reduction in injury and illness risks and liabilities. Today, most of the company’s claims are of a random nature, and the costs are no longer considered part of doing business.
Start Strong
Parking companies are not usually experts in this type of risk reduction, so the first step in a corporate prevention plan may be to hire an expert. For instance, PCI engaged Zoe Robinette, a risk reduction expert, who helped get the plan off to a strong start with immediate results. Robinette established quantifiable baseline metrics, which included the total number of injuries, dollars incurred, litigated claims, and annual dollars incurred on litigated claims. PCI kept it simple and purposefully chose not to measure subjective components, such as productivity, morale, and replacement costs. With the baseline set, PCI assessed its key metrics month over month and year over year. Many executives and managers were leery about one more risk reduction plan, but the immediate results earned their buy-in.
Be Specific
PCI worked with Robinette to create training materials that were specific to the type of injuries historically seen at the company’s work sites. Each week, PCI used the material to drill on current injury trends until the mechanism for injury was reduced and ultimately eliminated. The company used the successes as motivation to continue the process and continue drilling on those training methods to this day.
Target Zero
“A company’s target should be zero injuries and illnesses – anything less, you’ll miss the mark.” – Paul Gnasso
Risk reduction specialists have found that when companies set lower goals – such as a 50% reduction in risk – that’s all they achieve. A bolder target will lead to greater success. To achieve “target zero,” home in on specific risks and drill on prevention methods week over week. Celebrate victories and use failures to generate new drills for the playbook and further eliminate risks.
Level Up
A model of continuous review and improvement will help further reduce injury and illness. Robinette calls this the Level Up Process. Don’t stop at a companywide plan; once that plan is fully integrated into operations, individual locations, districts, or regions should develop their own prevention plans. These plans often introduce additional location-specific effectiveness. They may also offer creative ideas that can be implemented in other locations or as part of companywide operations. Use frontline eyes at the work site to pinpoint anything that could trip you up, literally and figurately. This includes uneven surfaces, illumination, areas requiring reflective tape, parking curbs – anything that could cause an incident for employees or visitors. Immediately address and correct the identified risks, which will advance the company’s culture of prevention. Finally, consider having an operational executive and your risk reduction expert conduct regular site safety audits throughout the organization. Treat these as opportunities to improve risk reduction rather than as opportunities to tell managers or employees that they have fallen short.
Beyond Incidents & Injuries
The best results come from a philosophy and culture that integrate the injury prevention process into business operations and make the results a component of corporate metrics. This culture starts at the top and works best when it includes managers and employees at every level and in various functions. Companies might reinforce this culture with wellness competitions, healthy lifestyle benefits and assistance, and other programs.
Validate Results
Validate the company’s employee health and safety achievements through objective measurements. Share successes with the entire company and use them as motivation to continue improving.
“While the idea of zero incidents and injuries may seem unattainable at the beginning of the process, it will feel very doable after a couple of years.” – Paul Gnasso
5 Key Steps to an Effective Risk Management Program
- Create a company philosophy and culture of injury prevention
- Have a Target Zero goal
- Outline specific measurement metrics
- Develop training manuals with issues specific to your business
- Establish continuous programmatic reviews
Read the full article here: https://mydigitalpublication.com/publication/?m=28381&i=742923&p=18&ver=html5
Visit our website at: Parking Concepts | We do so much more than just park cars